A ray of light
Miners face a dangerous work environment made more harrowing by conditions that make reliable wireless communications difficult, if not impossible.
November 1, 2007
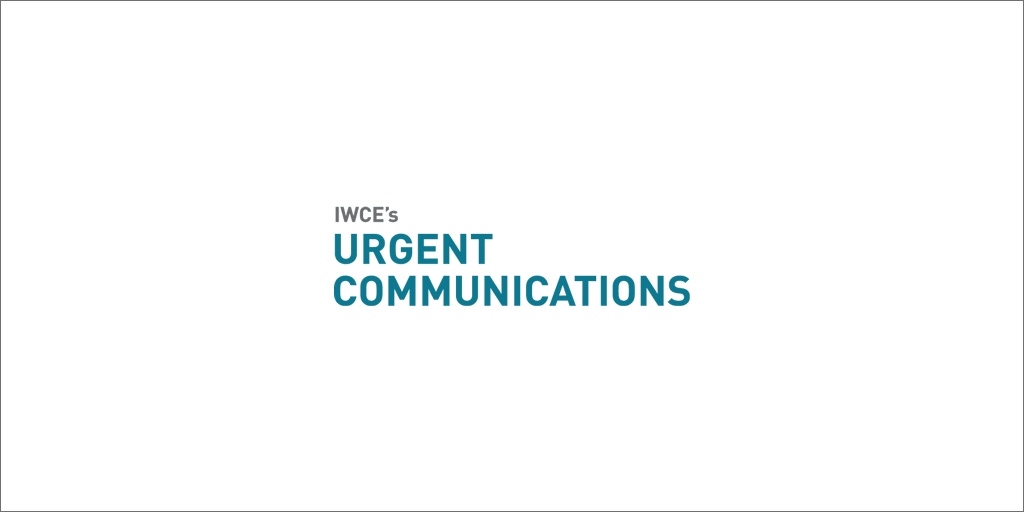
“Before you go under the mountain into the coal mine, you look up at the sky and wonder if that's the last time you'll ever breathe fresh air,” said Bob Hammonds, who worked in southeastern Kentucky's coal mines in the 1990s. “Every night when I went under the mountain that was my last thought. The next morning when I came up, looked out and saw the sun, I thought, ‘Whew, I made it.’”
Coal-mining is a dangerous job. Miners work thousands of feet underground beneath millions of pounds of rock. They are surrounded by high-voltage electrical lines, darkness, dust and highly explosive methane gas that seeps from the coal. Death isn't certain, but it's always a possibility, Hammonds said.
In fact, the Bureau of Labor Statistics' 2006 Census of Fatal Occupational Injuries reported fatality rates for coal-mining jumped 84% in 2006 to 49.5 fatalities per 100,000 workers, up from 27.8 in 2005 — much of which resulted from the Jan. 2, 2006, Sago Mine disaster in West Virginia that trapped 13 miners for nearly two days, killing all but one.
The Mine Safety and Health Administration (MSHA) responded to the Sago tragedy by sponsoring the Miner Act of 2006, which mandated coal-mine communication technology benchmarks. The act called for coal-mine operators to implement post-accident communications that provide a redundant means of communication with the surface for people underground. It also called for post-accident tracking systems that identify the location of all mine personnel who are underground.
Coal-mine operators now will be required to present a wireless communication plan to the agency no later than June 15, 2009, that defines the degree of functionality provided by the wireless two-way communications and tracking systems to be used to enhance miners' safety.
Congress seems to believe that new technologies may be the solution for mine communications, as evidenced by the $23 million it allocated to the National Institute of Occupational Safety and Health for the development of subterranean communication technology. Agency officials reported that 40 new communication and tracking systems supported by the funding are currently under review.
However, vendors face an uphill battle to pass MSHA inspections and meet manufacturing deadlines, said Dave D. Lauriski, formerly the U.S. Assistant Secretary of Labor for Mine Safety and Health and the head of MSHA under President George W. Bush from 2001 to 2004.
Potentially viable technologies must pass muster with the MSHA's Approval and Certification Center, which certifies products for use in underground coal mines. Among other standards, the technology must be intrinsically safe, meaning no explosion hazard under normal operations when used in gassy or dusty environments — especially in coal mines were large amounts of methane gas can accumulate. Following approval, a license is issued authorizing a manufacturer to produce and distribute products for use in coal mines.
Meanwhile, miners and their families question why communications systems aren't where they need to be — especially after the Aug. 7 disaster at the Crandall Canyon Mine in Huntington, Utah, where six trapped miners and three rescuers were left for dead 1800 feet underground.
“[Families] are taking the agency and mine operator to task over the adoption rate,” Lauriski said. “The simple matter is that the demand is greater than what can be produced right now, and it's going to take some time for the production and manufacturing levels to increase to supply communication devices for all mines.”
Currently, most mine operators deploy two-way radios and so-called leaky feeder systems for subterranean communications, Lauriski said. To allow radios to function underground, a standard surface antenna system is replaced with a cable network designed to “leak” a signal, letting radio signals both seep from and into the cable. The systems are used for both data and voice communications, he said.
Leaky feeder systems usually are hung at the top of the mine opening and intertwined with electrical conduit, said Joe Watts, Kenwood USA's senior product manager. In 2006, Kenwood's portable radios became the first to be approved by MSHA for use in underground mines. The company offers two models: the UHF/VHF TK-290 and TK-390. The ruggedized radios meet MIL STD 810 for dust and drops, as well as MSHA's intrinsically safe requirement.
MSHA also requires that the amount of stored energy in a two-way radio doesn't exceed a certain amount — making it an even more difficult challenge to provide reliable radio communications in coal mines, Watts said.
“I don't know of a perfect solution,” he said. “But a combination of voice communications with personnel accountability or location tracking might be the best solution, so if a disaster does happen at least you know the last location of those personnel.”
HAMMONDS' COAL-MINING days are over, but he stays involved by working with the Kentucky Community Technical College System on mine-safety issues, including wireless two-way voice and data communications. His team has developed a man-portable interoperable tactical operations center, or MITOC. The project was funded by a three-year, $1 million grant from the Department of Homeland Security through the state's National Institute of Hometown Security.
MITOC is a system of off-the-shelf, remote-communication devices housed in a suitcase-sized ruggedized case. An embedded BGAN satellite transceiver supports cellular, landline and Internet connectivity for 30 laptops and 36 voice-over-IP (VoIP) telephones. In addition, a radio module supports interoperability by linking disparate radio systems, and a vehicle-mounted VSAT meets higher-bandwidth needs, Hammonds said.
The case can be loaded on a plane, a boat, or a helicopter, or can be shipped commercially. “It can be sent anywhere and then with the flipping of a few switches can be up and operational in less than 15 to 20 minutes,” he said.
Hammonds also uses Rajant Corp.'s BreadCrumbs to set up a wireless-mesh network at an incident. The portable, battery-powered, self-healing 802.11b and 802.11b/g access points are placed at the entrance of the mine to create a wireless LAN. Then, rescue teams responding to an incident transport additional units as they progress into the depths, Hammonds said.
“GPS and GIS won't work underground,” he said. “Everything has to come back through a chain of communications inside to the outside of the mine.”
In addition, as additional access points are dropped, rescuers gain access to streaming data generated by myriad devices. “They will be able to wear sensors on their uniforms that take carbon dioxide [measurements] and will be able to carry a camera that will be able to show live, streaming video from the actual rescue team as they progress forward,” Hammonds said.
The access points pass standard IP traffic that can be carried over several backhaul technologies, said Glenn Booth, vice president of marketing for Rajant. In addition, coal miners can be armed with a mobile unit that attaches to their gear and automatically extends the wireless mesh network, provided it remains within the range of at least one access point, Booth said.
The system was approved in August by the West Virginia Office of Miner's Health, Safety and Training. West Virginia was the first state to implement new mandates after the Sago Mine incident and ordered all of its 202 underground mines to submit wireless-communication safety plans to ensure trapped miners can be located should an accident occur. Booth said Rajant's technology meets the state's mandate that operators must know the location of all miners immediately prior to an event via the use of tracking devices.
Active Control Technology also meets this mandate by providing mine operators with wireless two-way voice communications and a tracking system, said Steve Barrett, president and CEO. The company deploys a Wi-Fi network in a mesh-network configuration that operates on two frequencies. Each mesh node has four radios — two 5.8 GHz radios that provide backhaul connectivity and two 2.4 GHz devices that provide client connectivity. The nodes have a four-day, battery-powered backup system.
“It took 41 hours to find the miners in the Sago mine disaster, so we chose 96 hours as a standard battery backup,” Barrett said.
The signal is propagated through line-of-sight and uses a patented process and methodology to configure the directional antenna and nodes.
“The important thing when you build a mesh network is the range between nodes,” Barrett said. “It's critical that you maximize the range between nodes so you can really control capital costs.”
Barrett said the system is self-healing, automated and has a patented middleware solution that controls latency through multiple wireless hops on the network to the degree that the system supports video in addition to voice and data. In addition, the network supports several Wi-Fi accessories, including a Wi-Fi telephone that can be linked to a PBX and offers push-to-talk, paging, eight hours of talk time and 160 hours of standby time.
As part of the system, coal miners are armed with Wi-Fi radio frequency identification, or RFID, tags that are mapped to specific individuals and can be set to broadcast in seconds. To pinpoint users within a range of about 10 feet, location data are transmitted to a graphical user interface map of the mine to track movements of assets and miners in real time at the command-and-control level. The company also is pilot-testing Ethernet-based video cameras.
Barrett said the system hasn't been tested in its entirety because the company awaits MSHA sign-off regarding the agency's intrinsically safe standard, but he expects to receive approval later this year. However, the solution will cost from $200,000 to more than $1 million, depending on the size of the mine.
The low-power ZigBee protocol also is being tested for use in coal mines, said Jack Sun, president and CEO of Helicomm, because it supports large mesh networks. The company offers MineTracer, a ZigBee-based wireless data and tracking system.
“Most of the folks who try to address the problem of RF underground try to increase power to blast the RF signal farther, and unfortunately that has limited success in mining environments,” Sun said. “So the approach that we've taken to utilize ZigBee is that we have very low-power radios, and then we use a lot of them to establish an infrastructure that allows multiple routing paths and multiple means of communications.”
The system includes data radios and a network controller that sits in the mine office or at company headquarters. From that point, a serial communications bus is run into the mine — a wired communications backbone such as Ethernet, fiber or a leaky feeder can be used. Once in the mine, a subnet controller, or network manager, taps into the backbone, assigns addresses and maintains network communications.
At that point, all communications in the mine are wireless and access points scattered throughout the mine — typically about 200 to 300 feet apart — support redundancy and ensure there is no single point of failure.
In addition, intrinsically safe mobile transponders affixed to coal miners' gear report location data to the access points. “One of the beauties of the system is the mobile transponders,” he said. “We actually can interface them to equipment, so if you have a methane sensor, we can interface to the transponders to extract that information so you can know what the conditions of the mine are through that system.”
Mine operators can expect to spend $35,000 to $50,000 per mile for the system, Sun said.
ONE CRITICAL POINT these technologies don't address is transmitting radio communications during a mine disaster, where rock and dust not only trap miners but also create a veritable RF tomb in which signals quickly fade and then disappear. J.C. Miller, CEO and president of VitalAlert Communications, believes his team of researchers has found the solution to communicating under these circumstances.
The company offers through-the-earth communications that are interoperable with existing land mobile radio technology to support communications with miners or emergency workers who have entered the subterranean environment in the aftermath of a disaster. The technology transmits near-real-time, two-way communications through concrete, dust or debris using a very-low-frequency (VLF) system.
“VLF is a proven technology that's been used by the military for years and is a signal that actually allows a transmission to go through the earth,” Miller said.
He said the proprietary technology puts an RF signal in a virtual “envelope,” broadcasts it through the earth and then opens the envelope once it reaches the area where the signal needs to be propagated.
At the heart of the system are portable boxes, each supported by an amplifier and an antenna, that are placed both above and below ground. To build out a scalable system, several boxes would be required, similar to a cell system. Each box has a range that is defined by the geology, the amount of power needed and the size of the antenna used, Miller said.
During an emergency, coal miners could keep a box in the underground storage facilities where safety equipment is located.
“It would be a standalone unit where, if a rescue team is coming in, they can have an idea where the miners were and set up their equipment,” Miller said. “Depending on the mine geology, the depth of the mine and a number of issues relating to whether the communication comes from surface to underground or from horizontally, it would give them a range of coverage that they would be able to communicate two-way voice through the earth.”
But it hasn't been an easy road for the technology, Miller said. Currently, the system only operates at depths of about 650 feet — short of the average mine depth of 1000 feet. In addition, few in the industry are willing to test the technology, because many engineers are still stuck in the world of existing terrestrial systems.
“Mine companies tend to band-aid existing systems and try to use what's off the shelf. I really think that part of it is that they want it now,” Miller said. “The case here is that we have to embrace this, advance this and have a five- to 10-year vision. But when I talk to people, they say they want the technology to look like a cell phone. Well, that's not what it is. Maybe it will be there someday, but it's not where it is now.”
It's a reality that hits Hammonds hard. While he fondly remembers the camaraderie during his days mining coal, the tragedies in West Virginia and Utah bring sorrow to his heart. He empathized with all the families at the mine disasters who hoped for hours that loved ones would be found and, at the same time, anguished over questions of why communication systems were not in place to track personnel. And he watched on television as the overall lack of communications, stemming in part from a singular dependence on two-way radios, hampered rescue operations.
“Mines are still using the same technology they've used for years — there's no Internet access or wireless access inside the mine, just the leaky feeder and two-way radios,” Hammonds said. “Two-way radios have to be line-of-sight to work underground. They just don't work. There's just not an existing capability to do 100% wireless communications underground.”
PROXIM ACCESS POINTS TWEAKED FOR MINE COMMUNICATIONS
Proxim Wireless Corp. collaborated with Hannah Engineering on a wireless communications system that was approved in June 2007 by the state of West Virginia's Office of Miners' Health Safety and Training (MHST) for use in underground mines.
Hannah's Wireless Integrated Technology Systems, or WITS, solution is a fault-tolerant, self-healing communications and tracking system used within mines to send and receive voice, video, data and location information. It now incorporates Proxim's ORiNOCO AP-4000M wireless-mesh access points.
Robert Fitzgerald, CEO of Proxim, said the company identified the mining industry as a strategic vertical market, but originally focused only on open-pit — such as diamond — mines that do not need to meet intrinsically safe requirements.
That focus changed when Hannah approached the company and asked permission to modify its access points to meet the requirements of MHST and then meld them into the WITS system, Fitzgerald said.
WITS uses several of Proxim's mesh access points within a mine to send and receive information from the miners, foremen and maintenance crews. It is designed so if one access point is damaged, the signal can be rerouted to another access point, according to the company. The capability is enabled by Proxim's self-healing mesh technology that automatically reroutes traffic in the event a node in the network goes down, Fitzgerald said.
Hannah has submitted WITS to the Federal Mine Safety and Health Administration (MSHA) for intrinsic safety certification and anticipates that the system will be certified to be intrinsically safe by MSHA this month.
— Mary Rose Roberts
RATE OF FATAL OCCUPATIONAL INJURIES, 2006 (PER 100,000 EMPLOYED)
29.6
agriculture, forestry, fishing, hunting
27.8
mining
16.3
transportation, warehousing
10.8
construction
6.2
utilities
Source: U.S. Bureau of Labor Statistics, U.S. Department of Labor