How Hughes Network Systems could bring satellite-terminal manufacturing down to Earth
Satellite telecom has deep roots in Washington’s Maryland exurbs – the former COMSAT Labs building has been a landmark along Interstate 270 for decades – but in recent years, an unusual green shoot has sprouted up for the industry here: manufacturing.
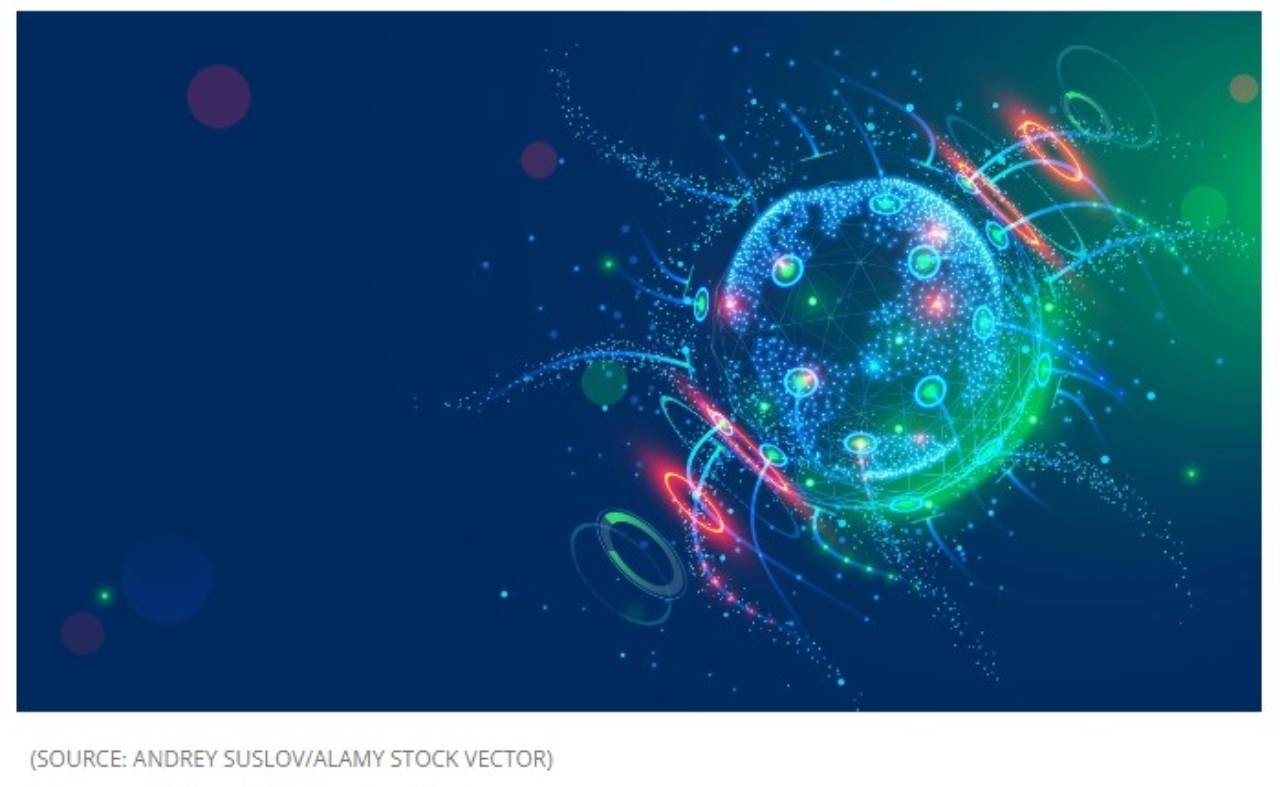
Satellite telecom has deep roots in Washington’s Maryland exurbs – the former COMSAT Labs building has been a landmark along Interstate 270 for decades – but in recent years, an unusual green shoot has sprouted up for the industry here: manufacturing.
By building satellite terminals in a factory opened just off that highway this year, EchoStar-owned Hughes Network Systems has chosen a different trajectory than that of competitors that still rely on outsourced production of consumer hardware even as the risks of overexposure to Chinese suppliers have become more apparent.
“We’re kind of a rare breed in Maryland, doing production work here,” said Eric Lee, senior vice president of operations and general manager at the facility, during an August 5 visit.
The building has just over 106,000 square feet of manufacturing space, in which 130 full-time employees and 200 contractors, most clocking into one of two shifts that run from 6 a.m. through 11 p.m., work with assistance from 50 robots to build terminals for Hughes’ own geostationary-Earth orbit broadband and for OneWeb’s low-Earth orbit satellite service.
“It’s very, very traditional manufacturing,” Lee said. “It’s not just a box build.”
On Tuesday, Hughes announced that it had shipped more than 5,000 HL1120W OneWeb terminals since it began delivering them in April. Those devices for enterprise and government customers use an electronically steerable antenna to communicate with the 618-satellite constellation that the British firm completed deploying in March. Hughes and OneWeb’s ties go back farther than that: In 2021, the EchoStar subsidiary participated in a funding round for formerly bankrupt OneWeb, which merged with Eutelsat in September.
Human-robot teamwork
A walk through the factory floor showed how Hughes has pushed the iterative adoption of automation to chisel away at its costs.
A line to build OneWeb receivers featured multiple handoffs from robots to humans. For example, after one robot applied a gasket compound around an antenna housing, taking just under 14 seconds to complete that task, humans took over to attach internal components. Then, humans tested the finished assemblies at a series of stations, including one under a tent just outside, where the hardware could pick up OneWeb’s satellite signal and employees could enjoy the sight of the landscaping next to the factory’s walls.
One finishing task, applying a hydrophobic coating to the exterior of the antenna that sent water droplets skittering away when I breathed on them, will soon be handed off to robots that will take the place of people with paint rollers.
“We first build six months, then we evaluate where the labor costs are going,” said Kamal Shah, senior vice president of operations and assistant general manager.
On another line, workers assembled indoor units for Hughes satellite customers – a job once outsourced to Chinese facilities.
To read the complete article, visit Light Reading.